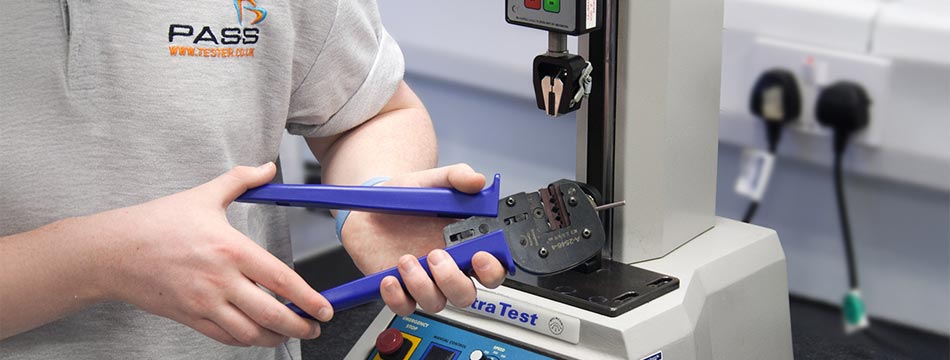
Calibrating instruments, tools and meters ensures that they generate correct results, and calibration is best implemented by laboratories able to provide UKAS certified calibrations carried out in accordance with ISO/IEC 17025:2005 standards.
Calibration is needed on many different types of mechanical, electrical and process industry tools. United Kingdom Accreditation Service (UKAS) is recognised by the British government to assess the competence of organisations that provide certification, testing, inspection and calibration services against internationally agreed standards.
In order to maintain UKAS accreditation, a laboratory is subject to periodic surveillance once a year and re-assessment once every four years. Accreditation provides valid and documented results which the customers can trust, which means reduced external audits for customers.
The advantages include proven traceability to national standards from a laboratory with able calibration technicians and approved signatories inspected by the assessors. The user has assurance that the equipment provides accurate measurement, is properly maintained and frequently checked.
Electrical Test Equipment
In the case of electrical instruments, PASS is now accredited to ISO/IEC 17025 on a scope of accreditation that includes AC and DC ammeters, bridges and similar resistance instruments, capacitance meters, charge amplifiers, frequency meters, insulation testers, loop testers, analogue and digital multimeters, portable appliance testers (PAT), power supply units, RCD testers, DC resistors and low frequency signal generators.
Basic function checks include whether every section of a tester’s display lights up, whether a continuity buzzer works and whether dials rotate freely. The three main types of single function 17th edition testers are loop testers, insulation/continuity and RCD testers.
To test a loop tester, a range of values between the minimum and maximum capability of the unit is applied. RCD testers must ensure they handle current according to manufacturers’ standards, by checking current output range, trip time and trip current.
For insulation and continuity testers, the output voltage for every insulation range must conform to manufacturer specifications. When testing continuity readings, every range is tested to ensure that the unit is zeroing correctly.
Flow meter calibration may be carried out on equipment such as anemometers and rotameters in a calibration laboratory, preferably in an accredited laboratory with a wind tunnel, or on-site at user premises. A laboratory should be able to calibrate all types of flow device including conventional flow meters, sensors and specific devices for measuring water, air and other types of flow.
Calibrating gas detectors and flue gas analysers ensures that gas equipment is working to specified accuracy within all relevant standards. Other gas equipment needing calibration includes quad gas instruments, refrigerant leak detectors and single gas instruments. Major gas tests include carbon monoxide, carbon dioxide, hydrogen sulphate, oxygen and methane.
Traceable calibration
Pressure calibration of all types of pressure devices may be performed, including pressure gauges, vacuum gauges, manometers and barometers with traceable hydraulic calibration equipment. When testing a gauge calibrate.co.uk conducts rising pressure tests and falling pressure tests, as well as minor repairs and readjustments of zero errors and range errors.
Temperature and thermometer calibration requires that technicians be able to perform calibration on-site in places such as industrial and chemical plants, hospitals, pharmaceutical and healthcare properties including NHS and private hospitals across the UK, as well as laboratory based calibration.
A thermometer consists of a measuring element such as a resistor or thermocouple, a conversion method such as resistance to temperature or electromotive force (EMF) to temperature, and the readout instrument or temperature indicator. A thermometer can be calibrated either as a whole system or by calibrating each subsystem separately.
In the case of a liquid in glass thermometer, the three components cannot be separated, so it is calibrated as a whole system. In the case of a resistance thermometer, the sensing element (resistor) can be calibrated separately by directly measuring resistance at various temperature points and the temperature indicator can be calibrated by applying known resistor values and checking the indication.
The crimping tools used within industries such as aviation and critical manufacturing processes need to be calibrated in accordance with standards to assure crimp security and quality. Controlling critical crimp dimensions is influenced by many factors including wire size and material variation and terminal size and material variation.
Common applications of torque wrenches include the automotive industry and piping applications, such as high pressure natural gas stations where the bolts used for flanged connections must be tightened according to the manufacturer’s specifications to avoid damage to critical equipment or causing a serious accident or gas leakage. The only sure way that proper torque is applied is to have the torque wrench calibrated.
Finally, weighing scales used in the medical and pharmaceutical industries, in the building sector and in the food industry, may lose their accuracy for a variety of reasons: sometimes their mechanical components may become worn out and cause a change in the reading. Environmental factors play an important role as well. There are two major categories of scales: automatic and non-automatic. Automatic weighing instruments are capable of performing consecutive weighing cycles without any intervention of an operator.
For further information, please visit calibrate.co.uk.